Increasing your pharmacy production capacity is an important part of growing your business
But there are a number of constraints that LTC pharmacies and Central Fill pharmacies face when it’s time to increase production volume capacity. Lack of space and limited personnel are two common factors that get in the way of growing your business.
The good news is that there are some solutions that make it possible to increase your pharmacy production volume capacity without moving to a larger space or bringing on additional personnel.
1. Get a space-saving automated strip pouch packaging unit
There is no question that automating part of your process can help you increase your production volume capacity. Automated strip pouch packaging has helped many LTC and Central Fill pharmacies significantly increase their capacity. However, much of the equipment created for automated strip pouch packaging is bulky and requires a lot of floor space. If you have a limited amount of space and no plans to expand or move, a large piece of equipment may not be a viable option.
If you are looking to increase production volume capacity in your LTC or Central Fill pharmacy without moving to a larger space, Noritsu has a solution – the Xana 2040. This compact piece of equipment has a footprint of just six square feet. It even fits through standard 24” doorways, which makes it quick and easy to install. The space-saving design of the Xana 2040 does not negatively impact speed, quality, features, or reliability when it comes to packaging medication. Features you can expect from the Xana 2040 include:
A white paper helps the long term care facilities see the value your pharmacy will provide. It is also common to include detailed data in white papers to help potential clients see the real value in your services.
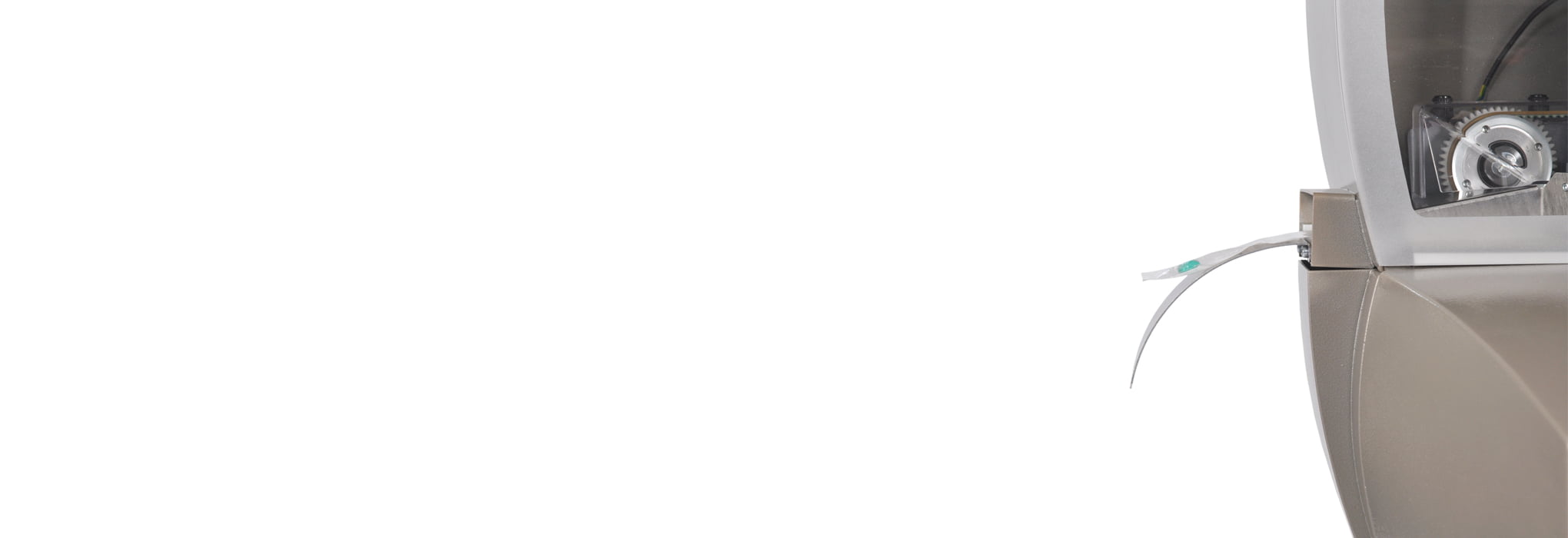
2. Maximize your efficiency with a medication detection machine
As an independent pharmacist for an LTC facility, there are regulations you must follow to remain in compliance with Medicare and Medicaid programs. Checking that the correct medication goes to the correct patient is an important part of compliance. When you set up an automated strip pouch packaging process, you’ll significantly increase your speed and production level. But manually checking medications can slow things down and limit your ability to increase your production capacity.
If you are looking for a way to speed up this process, consider adding a medication detection machine to accompany your automated strip pouch packaging unit. The MDM 1 from Noritsu is a compact medication detection machine that can image and verify up to 48 pouches per minute. You can even create a custom library using your own formulary to drastically reduce the number of pouches you have to check. The MDM 1 also has a space-saving footprint for pharmacies that want to increase production capacity but have limited space for equipment.
3. Eliminate the time-consuming process of hand-rolling strips
An automated strip pouch packaging unit and a medication detection machine will work together to make the process of packaging and checking the medication faster and more efficient. However, once the medication is packaged and checked, it still needs to be rolled and prepped for distribution. Hand-rolling can be both tedious and time-consuming, and it can really slow you down. This seemingly simple process will limit your production volume capacity.
Adding an automatic winder to your setup can significantly reduce the amount of time it takes to roll the pouches and help you increase production volume capacity at your LTC or Central Fill pharmacy. Options for winders include a tabletop hand winder, TPM exit winder, and a stand-alone winder. You can choose the one that fits within your space and works with your setup.
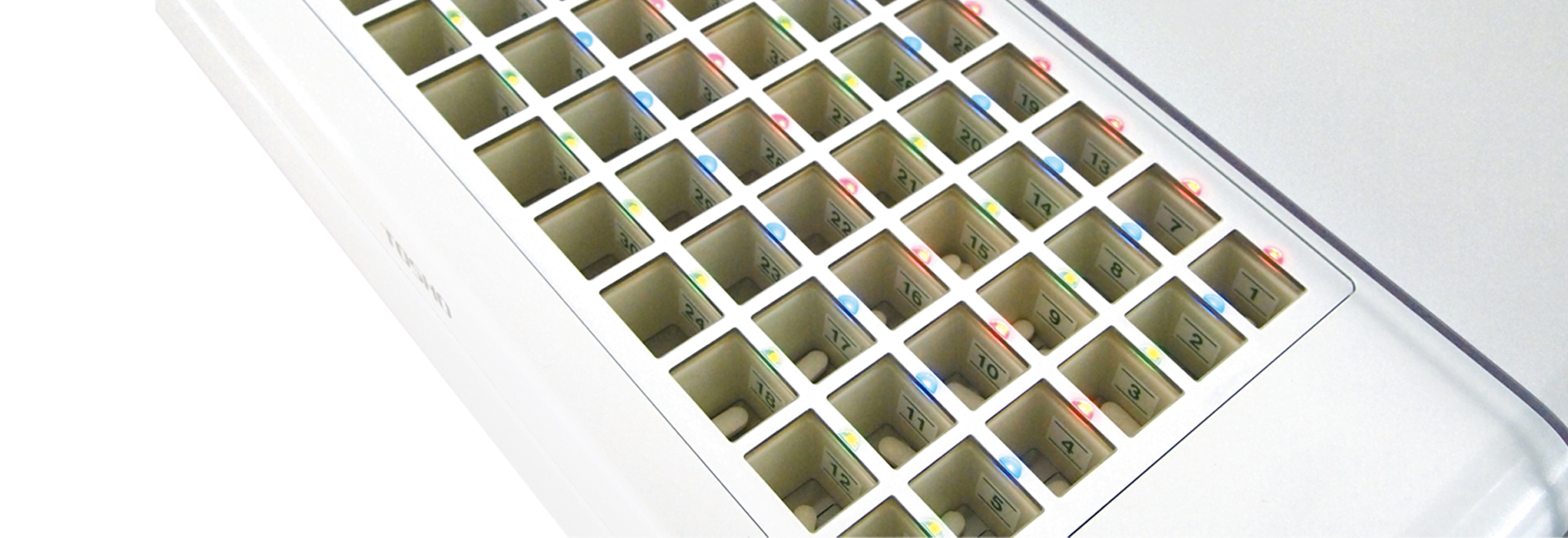
4. Quickly add less common medications without interrupting your workflow
Nothing will decrease your production capacity more than adding one-off, split-dose, and less frequently used medications. This interrupts your workflow and creates a bottleneck in your production process. Manually loading pills is time-consuming, and can lead to mistakes.
The Benjamin Tray System is designed to address these issues. This system works in conjunction with the Xana Pouch Packaging System to efficiently and easily add less common medications. You can pre-load the trays while the machine is in production, or prep multiple trays ahead of time to further improve efficiency and volume capacity. The Xana system will prompt the operator to use the appropriate medication when the time is right, so you don’t have to interrupt your workflow.
5. Streamline medication organization for efficient distribution
Once medication is packaged and checked, the next step is preparing it for distribution. Streamlining medication organization will make distribution more efficient and increase production capacity.
Getting the correct medication separated out for each patient is an important part of running an LTC or Central Fill pharmacy. This process can also increase compliance from patients, which is always top of mind for pharmacists in LTC and Central Fill pharmacies. Compliance and adherence products help you keep medications organized for each patient and make compliance easier. These include customized strip pouch boxes, strip pouch dispensers, and timed medication dispensers.
Increase capacity without relocating
With a little automation, you can increase the production volume capacity of your LTC or Central Fill pharmacy without hiring additional personnel or moving to a larger space. Noritsu offers a full line of automation solutions designed to help pharmacies grow and provide quality services to patients.
Are you ready to see what automation can do for your pharmacy? You can explore the Noritsu online store and request more information to learn about specific products that will help you increase the production volume capacity of your business.